Why should I buy a Walton Motorsport Exhaust Manifold?
Its time we put pen to paper (finger to keyboard) and came up with some reasons to use a Walton Motorsport exhaust manifold.
Specifically, we are talking about our core range of manifolds. We go through a few extra processes in their construction to ensure that they are the best on the market and a product that we are proud to put our name on.

The primary job of an exhaust manifold is to get the exhaust gasses out of the cylinder head and in the case of the turbo engine, past the turbos exhaust wheel whilst spinning it as quickly as possible. This is the easy bit of process, but we are going to talk more specifically about the strength and durability of the manifold, and also touch on turbo health.
We will start at the cylinder head end of the manifold, as that is where the exhaust gasses first enter the manifold. We design all of our head flanges in-house and have them Fiber Laser cut from 10mm thick 304 Stainless steel. We use 304 Stainless Steel for the full construction of our manifold to prevent corrosion. As the head flanges are welded they have a tendency to shrink. We take this into account in our design so that it still fits well. Importantly aligning with the ports correctly. The common shortcut to this is to use dramatically oversize mounting holes to account for the shrinkage. The issue here is that the flange will move around during mounting and not align with the exhaust ports correctly.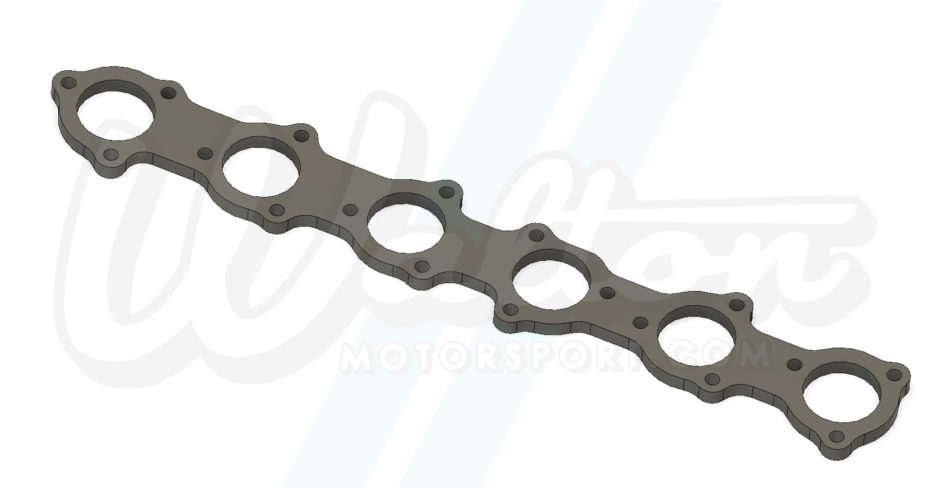
The Primary pipes are the tubes that go between the head flange and the turbo flange, Common practice is to weld the primary tube to the face of the manifold as virtually all our competitors do. Our method is to use a stub. This stub is a short piece of tube, which is pushed through the flange and welded front and back to create a super-strong base to support the turbo. The stub is how we tackle the problem of transitioning an oval exhaust port to a round tube. The below picture shows before and after welding. We of course port and flatten the flange after this process to ensure the best possible gas flow, along with a flat mounting face. This is a process that to the untrained eye is difficult to spot, you will generally know if a brand does this or not, because they will shout about it.
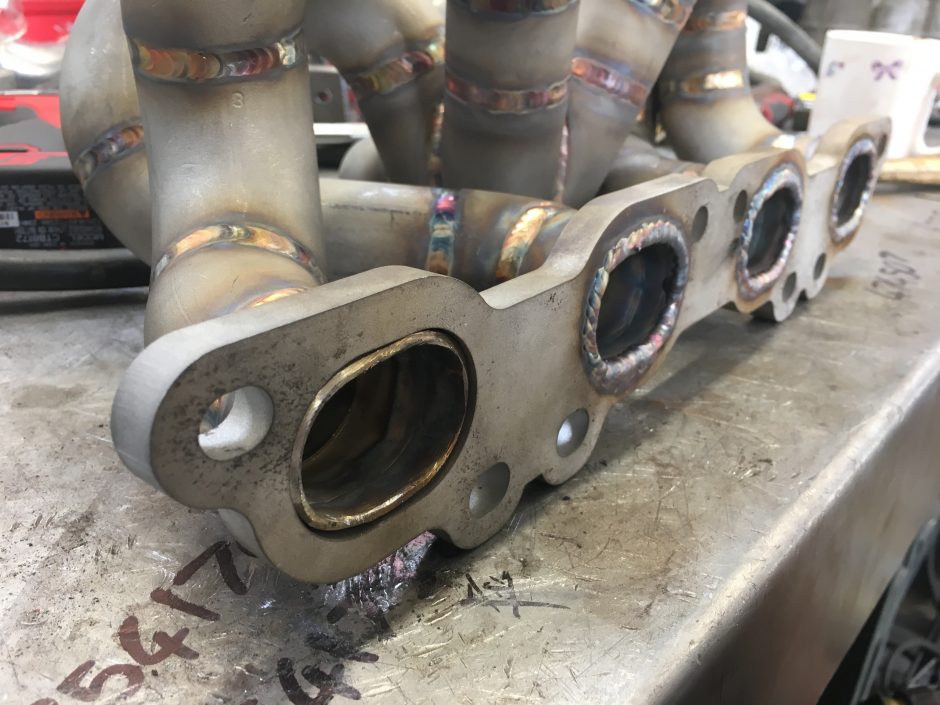
The primary pipes are then back purged and TIG welded, Back purging is the process of flowing Argon Gas (in the case of Stainless Steel) through the inside of the pipe, The argon creates a shield over the back of the weld preventing the molten metal from reacting with air in the atmosphere and creating a rough weld on the inside of the primary pipe helping to promote the best possible flow, we also like to keep the manifolds compact in the primary pipe routing but allow fitting to be as easy as possible and utilize stock studs and bolts where possible.
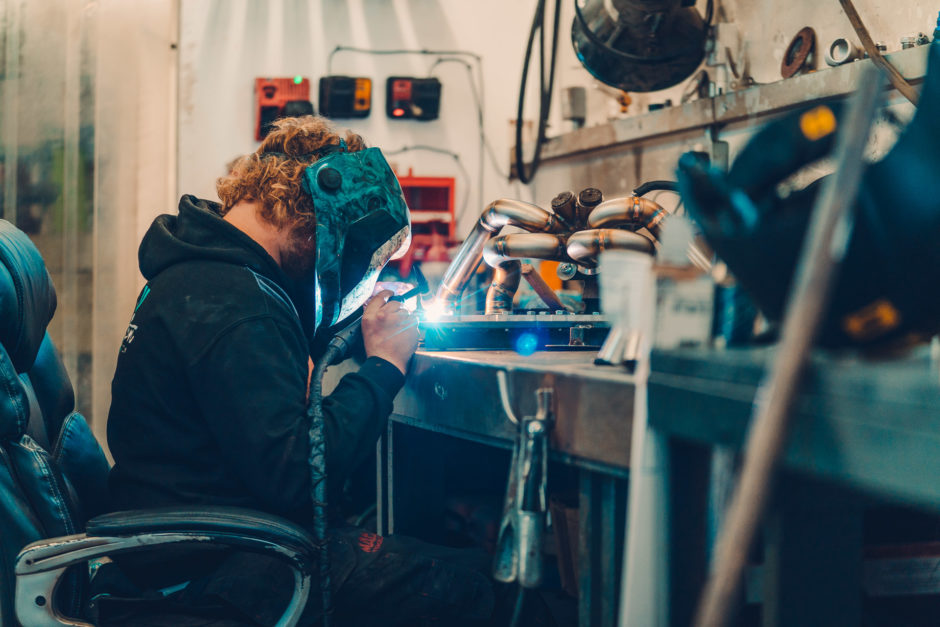
We are very proud of the fact that we design on produce out our merge collectors in house. A popular option in other brands is to use Billet CNC collectors. These can look really great aesthetically, however it does not allow such flexibility on design due to the nature of having to make them in batches to keep costs reasonable. Building our own collectors allows us to ensure each one is built to our quality standards and exact specifications allowing us the ability to modify design to suit each manifold and application. We weld our collectors internally and externally before porting the inside back to a smooth point. Most of our competitors don’t weld the inside, not only does this increase strength, but it eliminates the risk of metal fragments breaking off with the heat and making their way through your expensive turbo.

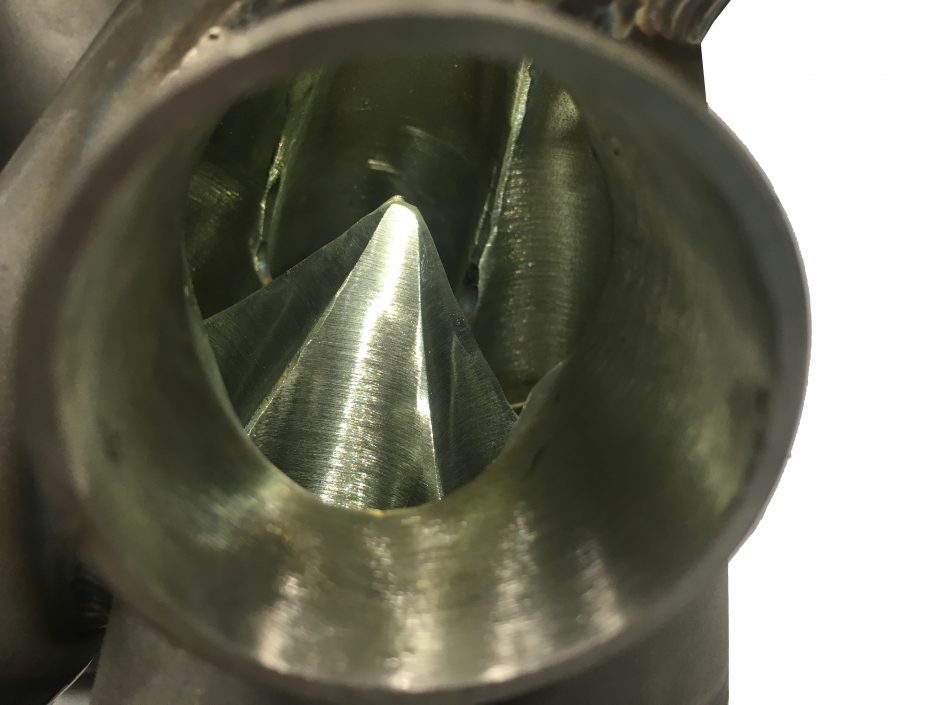
The Image below shows the internals of a failed collector that has not been internally welded, this particular manifold was one that we removed from our own R34 Skyline (fitted before we purchased the car) that had led to subsequent turbo failure when the particles passed through the propeller wheel.
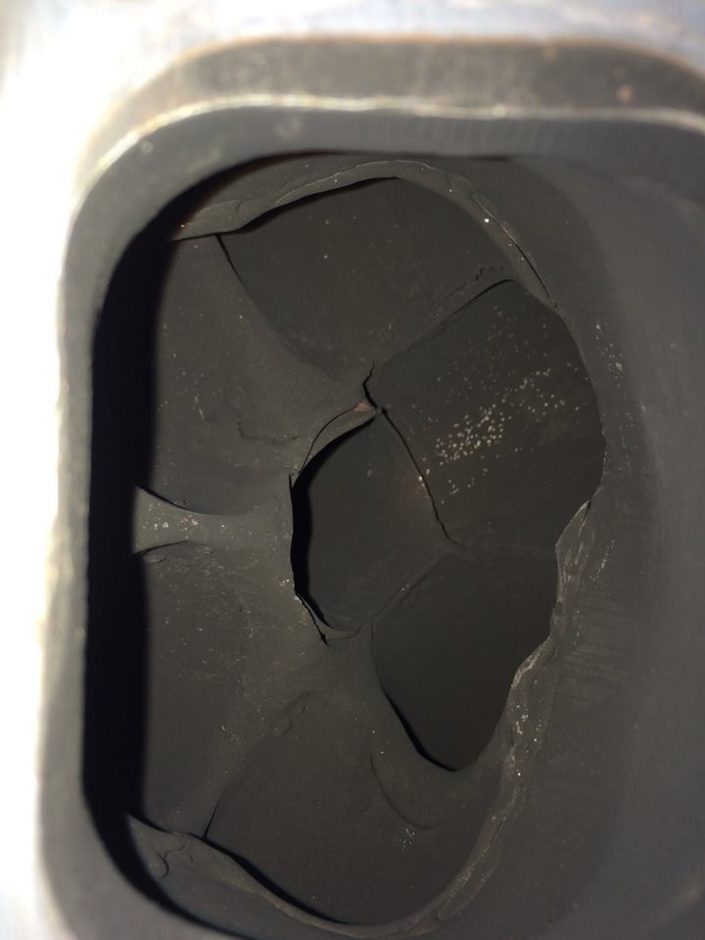
Although it takes more time, we keep the port in the flange to the correct shape of the turbo inlet, rather than taking the easy option and keeping it an oval shape. By utilizing the correct shape, this will of course give the best possible flow on our manifold for more power.

The Below photo is an example of an oval T3 port vs the correct shaped T3 port above. As used in our manifolds.
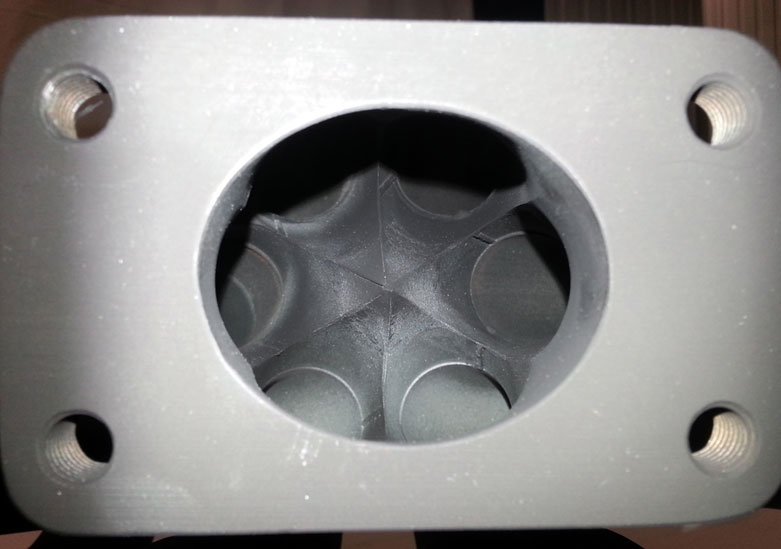
Introduced in 2019 was the improved waste gate port, Our current design using a curved waste gate port we are able to hugely increase the priority on the waste gate. This gives more control over your boost and turbo, as it allows a large of amount of exhaust gas to bypass the turbo (if required) but without upsetting the flow characteristics too dramatically. It also allows you to use a smaller (and less expensive) waste gate, but still maintain excellent control, We strongly recommend the Turbosmart Gen-V range of waste gates to compliment a Walton Motorsport exhaust manifold.

And of course we can accommodate any special requirements, twin scroll SR20? No problem, as featured on the Driftworks S15
We can also produce a manifold for any application, as well as using the super alloy Inconel 625, which is predominately used for F1 and Rally applications, As shown in this WRX Ford setup complete with fresh air antilag.
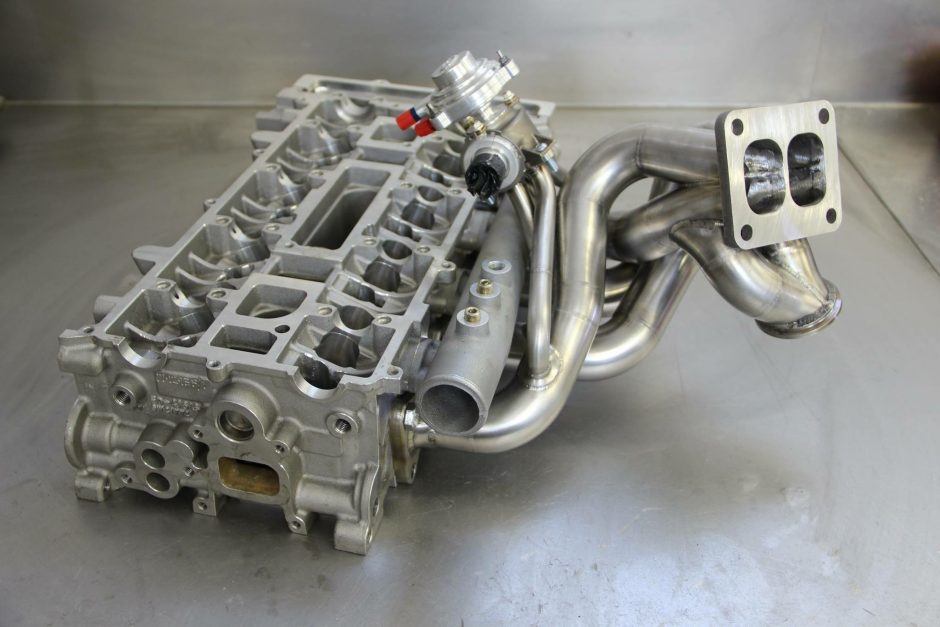
Lifetime Warranty
Most aftermarket manifolds offer this, offering the warranty is easy but the more tricky bit is eliminating the need to use it, if your manifold happens to break its great that its covered but its even better if it never failed in the first place, the extra steps that we have spoken about, help to significantly reduce the risk of a failure. The benefit of this is that you spend less time with the car in bits and a track day or drift day isn’t cut short.
We hope that this write up gives an insight into our manifolds that will help show the differences in the Walton Motorsport products.
For more information, don’t hesitate to pick up the phone, or arrange to come and see us and the products
01494 715206 – [email protected]